Understanding Porosity in Welding: Discovering Causes, Results, and Avoidance Techniques
As experts in the welding sector are well mindful, understanding the reasons, results, and avoidance strategies associated to porosity is vital for achieving robust and reputable welds. By delving right into the root triggers of porosity, analyzing its destructive results on weld quality, and checking out efficient avoidance techniques, welders can improve their knowledge and skills to produce premium welds constantly.
Typical Reasons For Porosity
Contamination, in the kind of dirt, grease, or corrosion on the welding surface area, produces gas pockets when warmed, leading to porosity in the weld. Improper shielding happens when the shielding gas, frequently made use of in processes like MIG and TIG welding, is not able to fully secure the liquified weld pool from reacting with the bordering air, resulting in gas entrapment and subsequent porosity. Additionally, poor gas coverage, typically due to wrong flow prices or nozzle positioning, can leave components of the weld unprotected, allowing porosity to create.
Impacts on Weld Quality
The presence of porosity in a weld can significantly jeopardize the general top quality and integrity of the bonded joint. Porosity within a weld produces voids or dental caries that deteriorate the structure, making it much more susceptible to fracturing, deterioration, and mechanical failing. These voids work as stress and anxiety concentrators, reducing the load-bearing capability of the weld and enhancing the possibility of premature failing under applied stress. Furthermore, porosity can also function as prospective websites for hydrogen entrapment, additional aggravating the destruction of the weld's mechanical homes.
Furthermore, porosity can prevent the performance of non-destructive testing (NDT) methods, making it challenging to find other defects or suspensions within the weld. This can lead to substantial safety concerns, specifically in vital applications where the structural honesty of the welded elements is critical.

Avoidance Techniques Introduction
Given the harmful impact of porosity on weld top quality, efficient prevention techniques are critical to preserving the structural honesty of welded joints. Among the main avoidance techniques is extensive cleaning of the base products before welding. Impurities such as oil, grease, rust, and dampness can add to porosity, so making certain a clean job surface is vital. Proper storage space of welding consumables in dry problems is also vital to avoid wetness absorption, which can lead to gas entrapment throughout welding. Additionally, choosing the suitable welding criteria, such as voltage, present, and take a trip speed, can assist lessen the risk of porosity formation. Making sure adequate protecting gas circulation and coverage is one more vital prevention technique, as inadequate gas insurance coverage can lead to atmospheric contamination and porosity. Correct welder training and certification are vital for carrying out preventive measures successfully and continually. By incorporating these prevention techniques into welding techniques, the occurrence of porosity can be considerably minimized, bring about more powerful and extra trusted bonded joints.
Relevance of Appropriate Shielding
Proper protecting in welding plays a crucial duty in avoiding climatic view it now contamination and guaranteeing the stability of welded joints. Shielding gases, such as argon, helium, or a blend of both, are generally made use of to protect the weld pool from responding with aspects airborne like oxygen and nitrogen. When these reactive components enter into call with the hot weld swimming pool, they can cause porosity, causing weak welds with minimized mechanical properties.

Insufficient shielding can lead to different defects like porosity, spatter, and oxidation, compromising the architectural integrity of the welded joint. Therefore, sticking to correct securing techniques is necessary to generate top notch welds with marginal defects and make sure the long life and dependability of the bonded components (What is Porosity).
Tracking and Control Approaches
Just how can welders properly monitor and manage the welding process to guarantee ideal results and avoid defects like porosity? By continuously monitoring these variables, welders can identify deviations from the ideal YOURURL.com problems and make immediate modifications to prevent porosity development.

In addition, carrying out correct training programs for welders is crucial for monitoring and managing the welding procedure effectively. What is Porosity. Educating welders on the value of maintaining constant criteria, such as proper gas shielding and take a trip speed, can assist protect against porosity concerns. Regular assessments and qualifications can additionally ensure that welders excel in surveillance and regulating visit the website welding processes
Moreover, the use of automated welding systems can boost tracking and control capabilities. These systems can specifically control welding parameters, lowering the chance of human mistake and making certain regular weld top quality. By incorporating sophisticated tracking modern technologies, training programs, and automated systems, welders can successfully monitor and regulate the welding process to lessen porosity problems and attain top quality welds.
Verdict
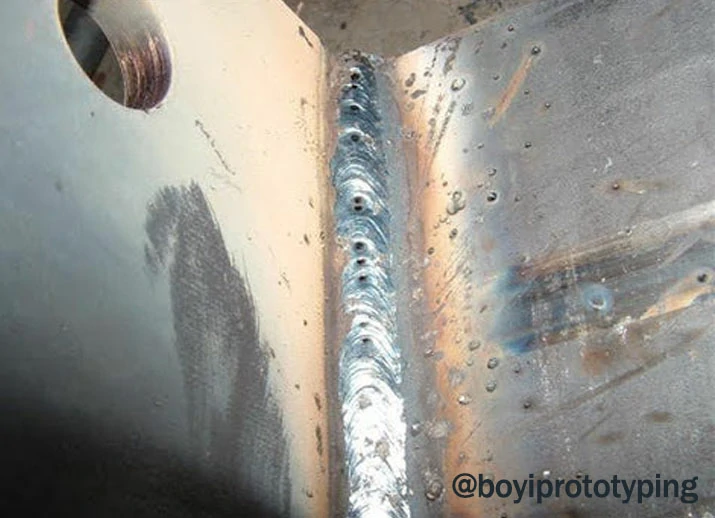